Pros and cons of PSV testing methods
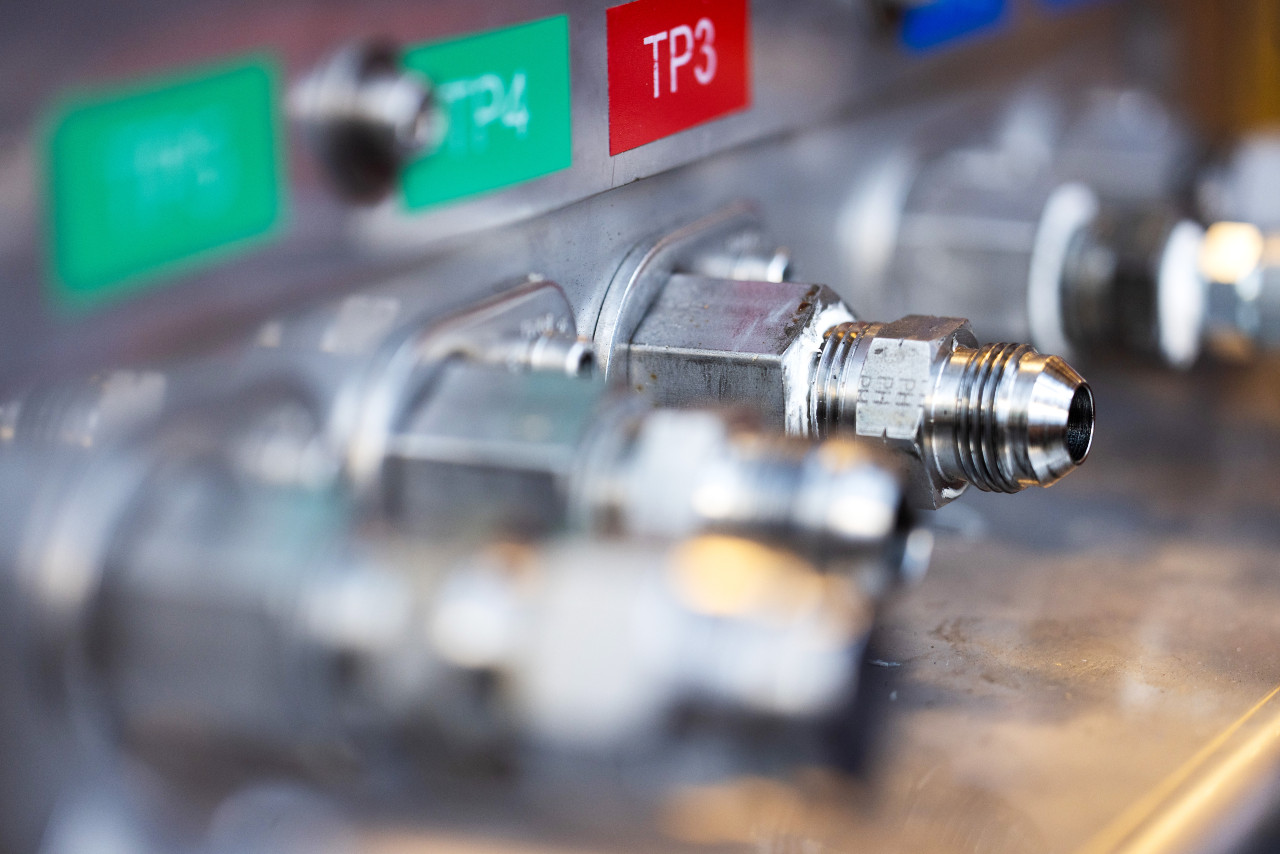
Several methods are used for testing PSVs. Here’s an overview of the different ways to do it and an assessment of their advantages – including Inline X’s patented method.
The Pressure Safety Valve is the last line of defense when it comes to protection against potential overpressure accidents at any site processing gas and liquids under pressure. To ensure functionality, all PSVs are regularly inspected and overhauled. But what are the most common methods used to test PSVs? And what are their pros and cons?
The recommended practices
Globally there are several million PSVs in service, so the need for a "best practice" is significant. Several organizations have issued Recommended Practices (RP) onPSV testing; where the American Petroleum Institute is one of the most common in Europe.
API has issued two documents that describe the process of ensuring a PSV is functioning:
- API RP576 describes the inspection
- API Std527 defines the Seat tightness test
Working according to these is recommended and even mandatory in most countries globally, even if it is only a recommended practice. There is room for several methods for inspecting PSVs and ensuring they are fully functional through testing.
A sequence of tests is required to thoroughly ensure that the PSV opens at the correct pressure and is not leaking. Often it is desired to also examine the current state of the PSV by performing an initial seat tightness and set pressure test.
The workshop test
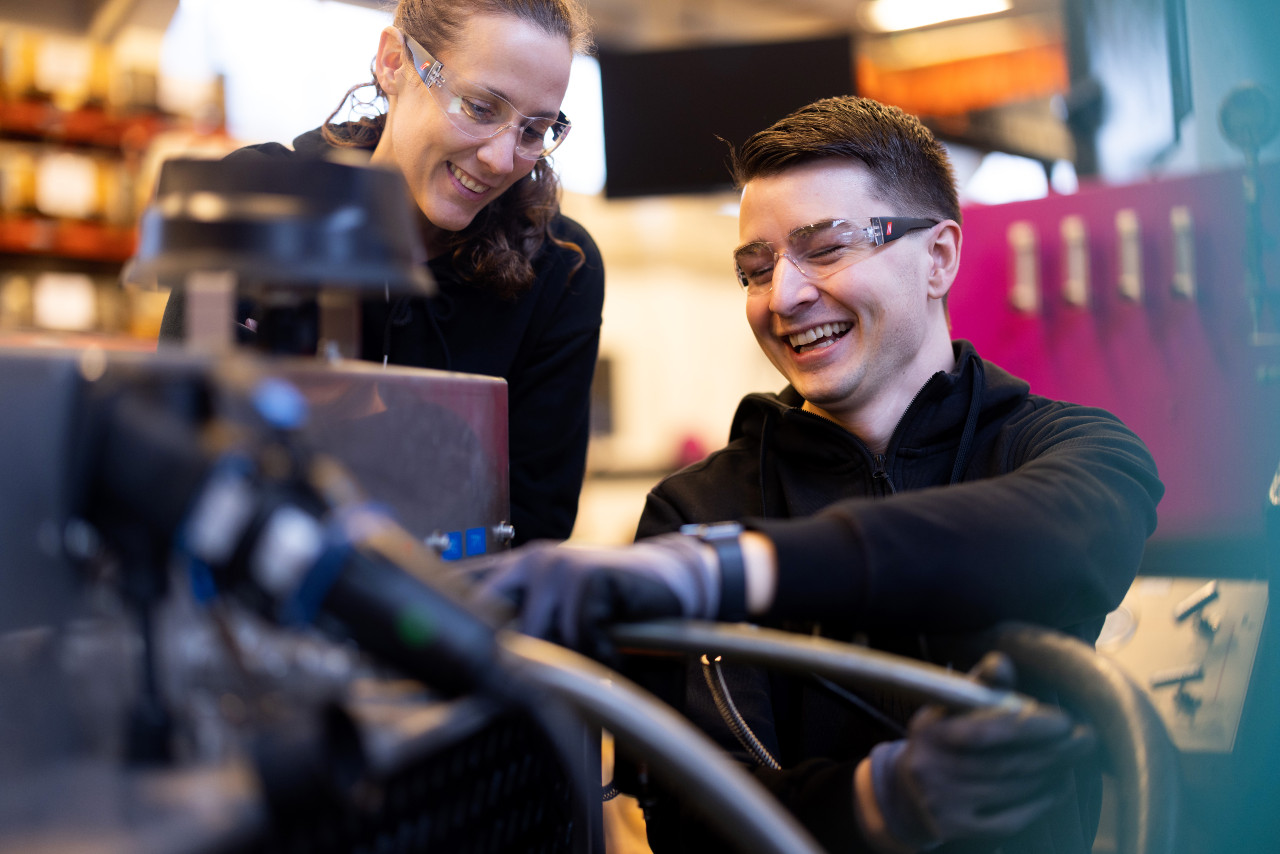
Following the examples given in the API, the most common practice of testing PSVs is to perform the test on a test bench.
To do that, each PSV needs to be dismounted and transported to a workshop. The PSV is mounted on a test bench in the workshop, and all the tests are performed. If the PSV is in good condition, it is transported and put into service.
Pros
- A well-known method with a long history
- It is convenient to test with spare parts close by should there be a problem
- Low inlet volume leads to low test medium consumption
- Good opportunity for visual inspection
- Possibility to use both liquid and gas as the test medium
- High range of the set pressures that can be tested
- Can test seat tightness and back pressure
- Can test pilot and bellow type PSVs
Cons
- The "as received" status of the PSV cannot be known as dismounting and transporting – it may impact the function
- The integrity of the valve is risked as the newly tested PSV needs to undergo transportation and mounting before it can be put back into service
- Repeatability of a test is often left to the human operator
- Risk of injury and potential accidents when dismounting and transporting a PSV
- Manual work is often required to note the results and enter them into a system
- It does not give any information on the state of the Isolation valve
- Potentially shutdown dependent or requires a non-passing isolation valve
The mechanical spring test
As the mechanical structure of a conventional PSV is as simple as a spring holding a disk tightly in place, testing the PSV by lifting the stem using a hydraulic system indicates the load at the point of opening.
Using force sensors and mechanically lifting the disk from the seat is a method that can be used in situ without dismounting the PSV. Knowing the pressure and volume of the inlet pipe segment makes it possible to estimate the force needed for the PSV to open. It can then be adjusted to get a load at the point of opening that will match the set pressure.
Pros
- It can be performed on-site without a full dismount and transportation of the PSV to the workshop
- High repeatability as the test procedure is automated
- It can be used for most set pressures
- It can be used without isolation of the PSV
Cons
- Cannot perform seat tightness test or back pressure test
- Cannot perform a set pressure test of Pilot or bellow type PSVs
- Does not pressurize the valve seat with gas/Liquid pressure
- Requires information that can often be hard to get by, e.g. current inlet pressure, inlet pipe segment volume, and disk area
- Manual work is often required to note the results and enter them into a system
- It does not give any information on the state of the Isolation valve
The bottle & pressure gauge test
Many PSVs have an isolation valve and a bleed valve on the inlet side to facilitate dismounting. This way, the PSV can be taken out of service by closing the isolation valve and draining the inlet volume via the bleed valve.
The bottle & pressure gauge test uses the bleed valve to connect a manometer and bottle of nitrogen to manually build up the pressure in the inlet volume until the PSV pops. The relief pressure is then found by listening for the pop or when the pressure build-up stagnates.
Pros
- It can be performed in situ with no need for dismounting and transportation
- The components needed to perform the test are readily available
Cons
- Cannot perform seat tightness test or back pressure test
- Requires isolation and bleed valve on the PSV inlet side
- The repeatability of a test is up to the human operator and therefore challenging to ensure
- Increased HMS risk compared to the other methods
- Manual work is often required to note the results and enter them into a system
- It does not give any information on the state of the Isolation valve
- Requires high-pressure nitrogen bottles
- Requires a non passing isolation valve
The Inline X in situ test
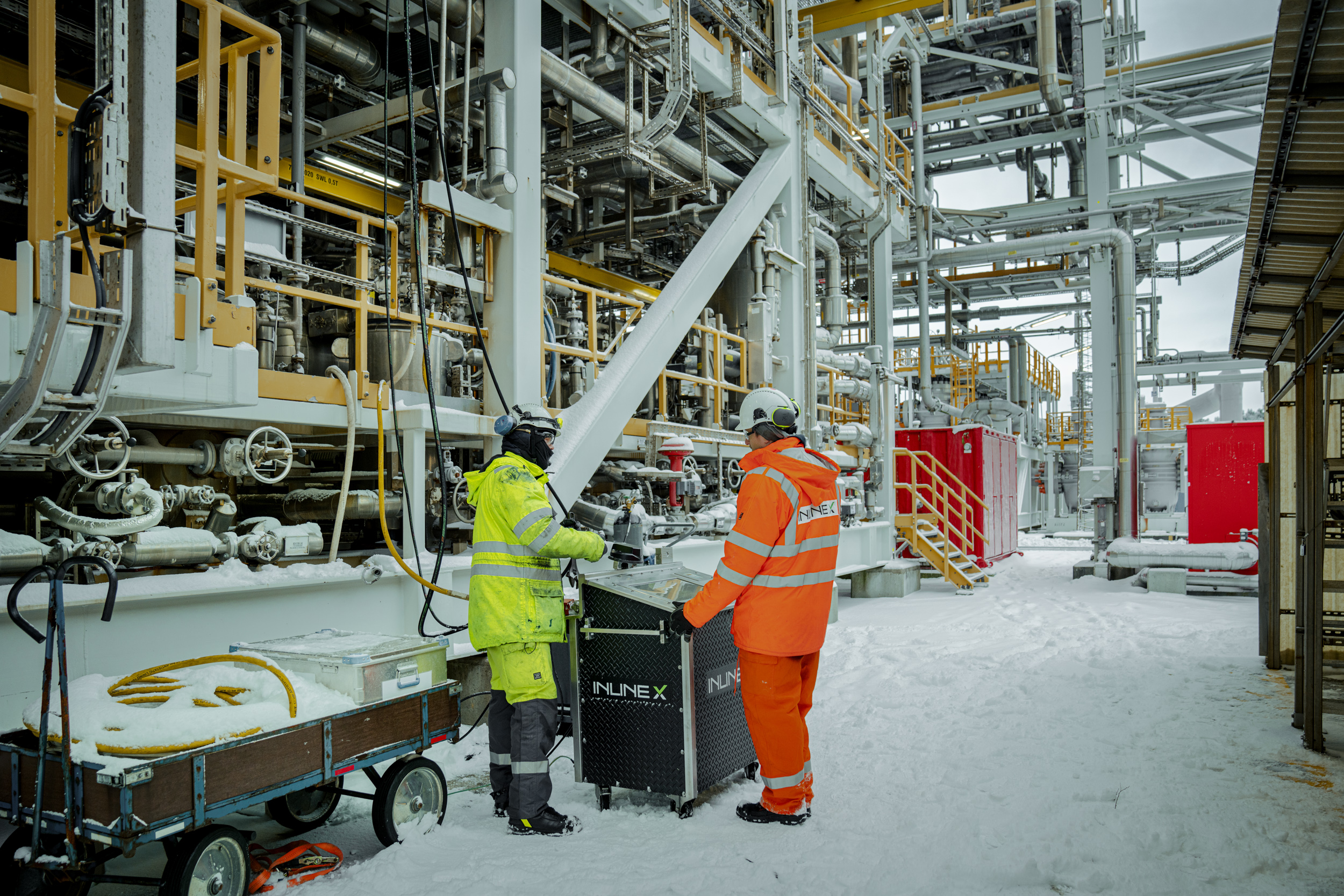
The patented method to test a PSV via the bleed valve is done with a test unit filled with sensors, actuated valves, and computers. Via a built-in touch screen, the operator can control the test operations while getting continuous data on the status of the test.
The operations are automated and do not rely on the human factor for repeatability. In addition, the complete test result, including all sensor data, is uploaded to the cloud for easy and detailed access to the results.
Pros
- It can be performed in situ with no need for dismounting and transportation
- High repeatability as the test procedure is automated
- Easy to use due to the automated test sequence
- Can test seat tightness and back pressure
- Gives status of the isolation valve by testing the leakage
- Can test pilot and bellow type PSVs
- The initial test will show the “as received” status of the PSV
- Test results are made accessible minutes after testing is completed (as long as there is internet access)
- Safety systems are in place to provide maximum protection for the operator and PSV
Cons
- Requires isolation and bleed valve on the PSV inlet side
- Requires instrument air, nitrogen, and power
Summary
Ensuring that each PSV is always fully functioning and using minimal resources is challenging. Selecting a suitable method for testing is an essential step in this process, but whenever possible, testing the PSV in situ will always be the best way of knowing the “as received” status and ensuring that the PSV put back into service is fully functioning.
In the end, a combination of workshop and in-situ testing is demonstrated to give a highly sustainable effect by optimizing cost, reducing risk, and increasing the overall valve integrity.